Helping people understand bionic technology is part of our core mission. In this article, we examine the potential of soft bionic hands.
The Need for Improved Durability
As anyone who owns a bionic hand knows, durability is still a problem. Our User Satisfaction Surveys show that even recent versions of leading bionic hands continue to break at troublesome rates. This causes end-users a significant amount of frustration and inconvenience. It also affects their confidence in their prosthesis.
Most commercial bionic hands are currently made with rigid mechanical parts. Some companies have tried to improve durability by using stronger materials, such as titanium. Others have added cushioning and increased joint flexibility. Yet, the problem persists.
One possible solution is to use soft robotic design principles.
What Are Soft Robotics?
As usual, let’s start with a short video overview. Note, this particular video is about robots, not bionic hands, but don’t worry. We’re just trying to establish a few design principles first:
So, in essence, we replace all the rigid mechanical parts with soft material, which we then move using cables, hydraulics, pneumatics, electricity, or even chemical energy.
This makes sense for something that moves like a fish or snake, but what about a hand?
Applying Soft Robotic Principles to a Bionic Hand
This video lacks voice narration but clearly demonstrates the feasibility of using soft robotic technologies in a bionic hand:
Here are the key design elements of this hand:
- It is entirely 3D-printed, including any requisite structures/joints.
- The fingers are controlled by an artificial tendon (i.e. small cable), as you can see in the following diagram:
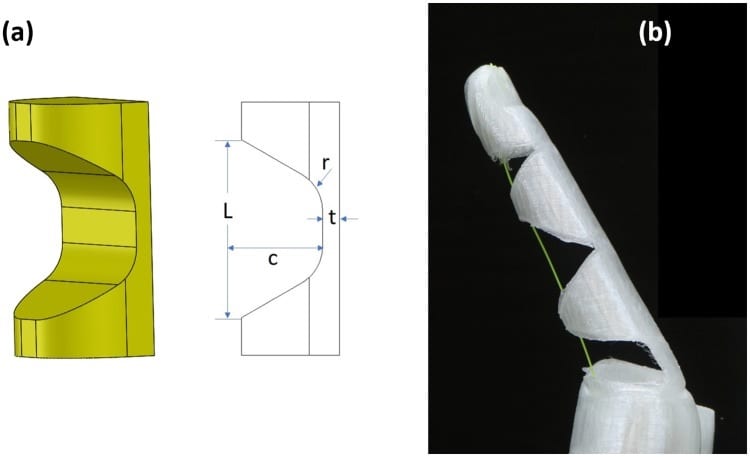
- The motors, microcontroller, etc. are placed in the palm:
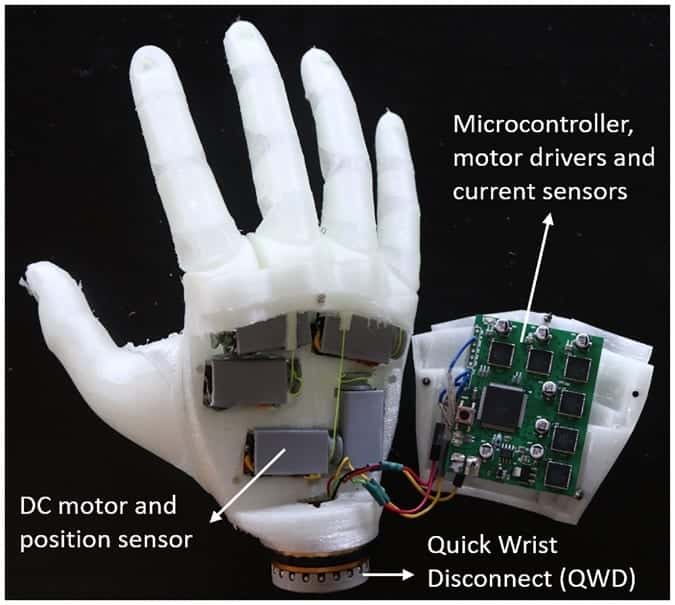
- The fingers and in fact the entire hand are then enclosed in a 3D-printed membrane, which could make the hand both waterproof and dustproof:
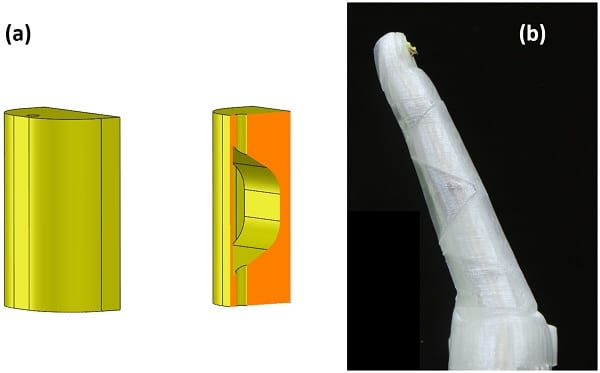
- The hand is controlled using two myoelectric sensors to open and close its thumb and fingers.
- Only three core grips are supported; switching between the grips is achieved via a tactile button, not myoelectric control.
- The hand is much lighter than all existing commercial hands, with a total weight of only 253 grams; this is about half the weight of a bebionic hand or an i-limb, and nearly 40 % lighter than a typical male natural hand.
Put another way, you are looking at a much lighter, more durable, greatly simplified design compared to most modern bionic hands, yet one that is still capable of successfully performing many daily activities.
Note, the hand featured in this section is the X-Limb, which you can read more about here. Also, all images in this section are from the scientific paper, A practical 3D-printed soft robotic prosthetic hand with multi-articulating capabilities.
However, this is not the only example. This next video demonstrates an inflatable soft robotic hand that gives amputees real-time tactile control:
Built by the Massachusetts Institute of Technology (MIT) and Shanghai Jiao Tong University, the palm is entirely 3D-printed. The fingers are balloon-like, each embedded with fiber segments similar to the articulated bones in natural fingers. To move the fingers, a simple pneumatic system precisely inflates them to bend them into specific positions.
This eliminates the need for mounted electrical motors for each finger, significantly reducing costs. In fact, the total cost of components for the entire hand is around $500, and that includes sensory feedback from pressure sensors in the fingertips! Additionally, because the hand has fewer moving parts and is made from a soft, stretchy material known as EcoFlex, it has the potential to solve the durability problem that plagues so many commercial bionic hands.
For control, the hand basically uses the same type of myoelectric control system used by most current bionic hands.
And how does the hand perform? In one test, two volunteers were given 15 minutes of training. They were then asked to perform several standardized tests to demonstrate manual strength and dexterity. When they repeated these same tests using a more rigid, commercially available bionic hand, they found that the inflatable hand was as good or even better at most tasks compared to its rigid counterpart.
This is a very exciting area of research!
The Potential Use of Artificial Muscles
Of course, the moment you start moving away from motors and actuators to power hand/movement fingers, you inevitably encounter the subject of artificial muscles. In this specific case, we mean using artificial muscles to move a soft robotic hand, as demonstrated by this intriguing project by Automaton Robotics:
This particular device is powered by a compressor about the size of a briefcase, so it isn’t feasible to use as a bionic limb (it will more likely make its way into robots first). But we wanted you to see the potential speed, fluidity, and strength of movement when combining this type of technology with soft robotics.
Drawbacks of a Soft Bionic Hand
Currently, there are two main drawbacks to soft bionic hands:
- Absent the kind of artificial muscles in the preceding video, the grip force is much weaker than that of commercial bionic hands, especially when using a power grip.
- The sophistication of current soft robotic hands is also inferior when compared to the leading bionic hands currently on the market. The number of available grip patterns, automatic grip adjustments, etc., are areas that soft robotic hand simply haven’t turned their attention to yet. But once the basic power and motion issues are resolved, we see no reason why soft robotic hands shouldn’t be able to replicate this more advanced functionality.
Why You Should You Care About This Technology
One of our main goals at BionicsForEveryone.com is to make those with limb differences aware not only of their current commercial options but also of new options in development. We do this because we recognize that many end-users are trying to plan cost-effective strategies for their future prosthetic needs.
The idea that a bionic hand may be available that:
- can be entirely 3D printed;
- cost less than $500 in parts, meaning it might eventually sell for only a few thousand dollars;
- is inherently durable and completely waterproof and dustproof.
…well, that’s just too compelling to ignore!
Related Information
For a list of competitor devices, see current options for bionic hands.
For a comprehensive description of all current upper-limb technologies, devices, and research, see A Complete Guide to Bionic Arms & Hands.